CNT Synthesis
Carbon Nanotubes (CNTs) possess exceptional electrical, mechanical, thermal and optical properties. These properties have enabled have enabled a vast array of applications across all multiple disciplines of science and technology. However adoption of many of these technologies has been slow due to the difficulty of producing large amounts of high quality CNTs. Improvements in CNT synthesis technology promise not only to enable many of these applications, but will also to provide a potential method for fixing carbon derived from natural gas or biogas in an economically valuable form.
The Pasquali lab is currently researching floating catalyst chemical vapor deposition (FCCVD) synthesis of CNTs from methane. FCCVD. Our primary goal is to developing an efficient, scalable process for producing large amounts of long, highly crystalline CNTs, with net positive co-production of hydrogen. In pursuit of this goal we are studying the internal thermal and chemical environment of the FCCVD process in order to better understand and control the complex interactions between reaction kinetics, thermodynamics, and transport phenomena within the reactor.
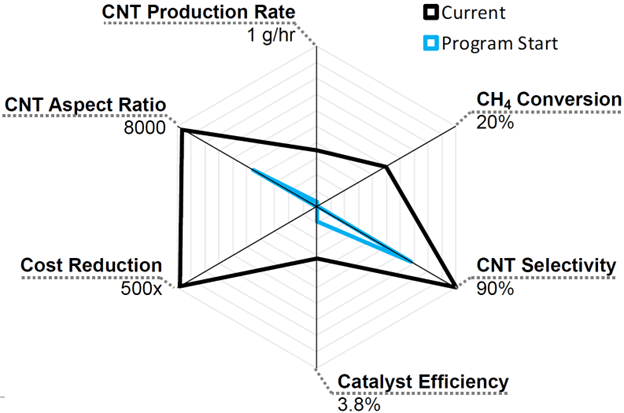
CNT Fiber Spinning
High-performance carbon nanotube (CNT) materials such as fibers and films can displace steel and other metals (e.g., aluminum, copper, and iron) – major offenders in terms of energy consumption and CO2 footprint – in a broad range of applications. The Pasquali Lab at Rice University is a world leader in technologies underlying CNT fiber spinning, a method similar to that used for the production of polyethylene (Dyneema and Spectra) and aramid (Kevlar and Twaron) fibers, as well as the precursors of carbon fibers. CNT fiber spinning is particularly attractive because it decouples fiber production from CNT synthesis and can deliver high-quality fibers at scale.
A recent article by the Pasquali group reported on the latest properties of solution-spun CNT fibers with a tensile strength of 4.2 GPa (specific strength of 2.1 N/tex, or ~55% of IM10 carbon fiber) and electrical conductivity of 10.9 MS/m (specific conductivity of 5640 S.m2/kg, or ~85% of copper). The incorporation of such high-performance CNT fibers into products is particularly appealing for applications where materials need to combine outstanding properties with light weight and flexibility, like those often encountered in the aerospace, automotive, electronics, robotics, power transmission, biomedical, and telecommunications industries. However, the ultimate adoption and incorporation of CNT materials into products and applications will require large-scale production at lower cost, higher efficiency, and strategies for managing their end-of-life. Current research efforts focus on improving both the scalability and sustainability of CNT fiber production. Examples include studies of alternative combinations of solvent/coagulant for CNT solutions, CNT materials produced from mixtures of CNTs synthesized by different methods, and recycling of CNT materials with predictable properties.
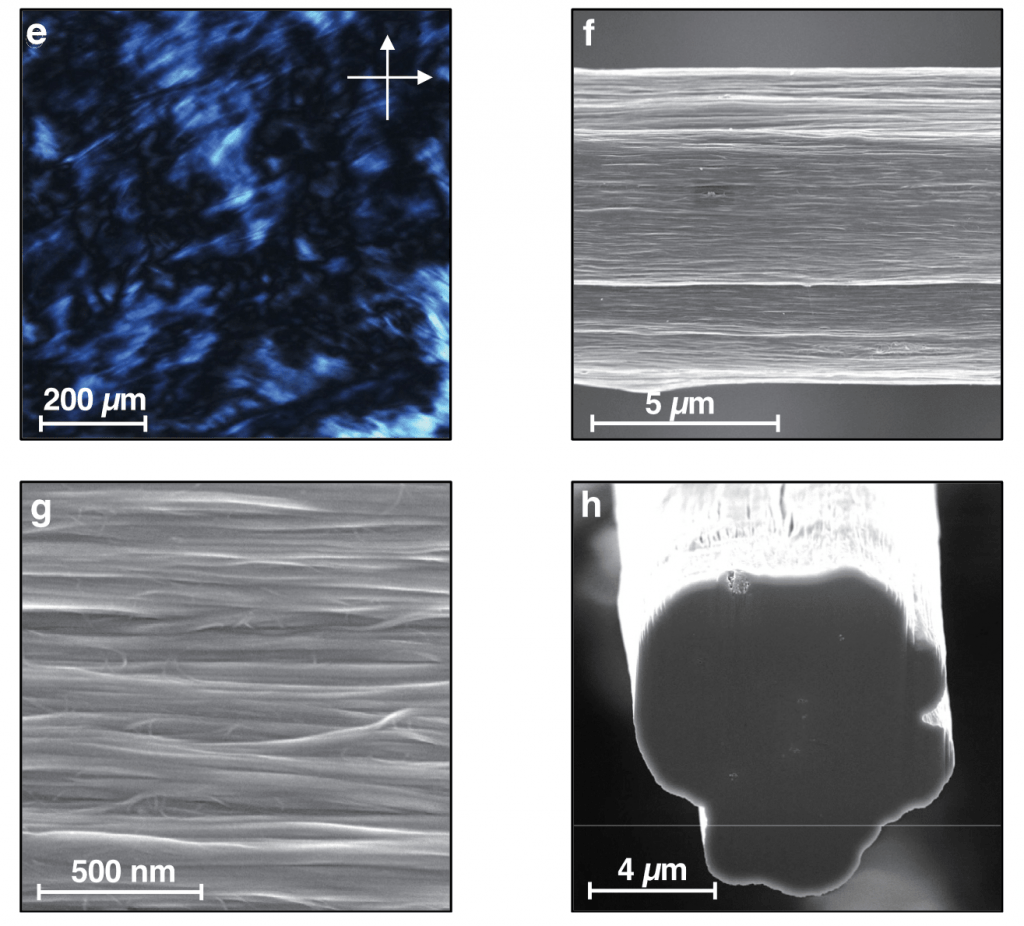
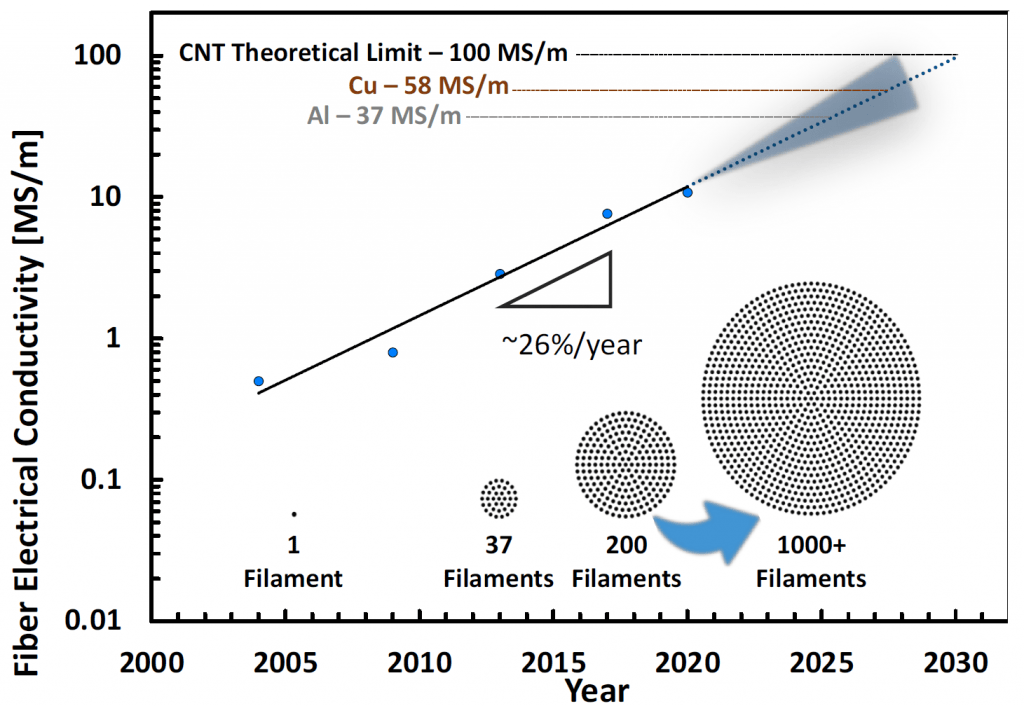
Boron Nitride Nanotubes (BNNTs)
Structural analogs of CNTs, boron nitride nanotubes (BNNTs) share many of the favorable properties of CNTs (e.g., low density, high strength, high thermal conductivity) with some key differences. Unlike CNTs, BNNTs are neutron shielding, electrically insulating, and stable in air up to 900 °C. This unique combination of properties makes BNNTs perfect candidates for the demanding conditions found in aerospace, where material integrity at extreme high and low temperatures is critical.
The Pasquali lab is currently researching BNNT purification, BNNT liquid crystal formation, and adapting existing wet spinning techniques for the production of macroscopic BNNT materials, like thin films and fibers. With a delay of ~20 years relative to research on CNTs, we now seeing the solution-processed neat BNNT materials become a reality. The the prospect of high-performance BNNT materials will soon be attainable if BNNTs continue to follow the pace of development set by CNTs.